Heat pipes are passive devices used to transfer heat in closed-loop systems and are commonly found in heat recovery units, spacecraft thermal control, and electronics cooling. A heat pipe transfers heat by harnessing phase change and capillary action within a sealed, evacuated tube containing a wick and working fluid. The tube’s material should have high thermal conductivity, and the wick structure must move the working fluid from the cold end to the hot end of the heat pipe.
The fluid within a heat pipe needs to have a low boiling point and a high latent heat of vaporization. Copper piping is often paired with water, and aluminum with ammonia. Heat pipes are common in HVAC systems, electronics, and aerospace vehicles. Some variables, including the wick structure, working fluid, and operating temperature, can impact how well heat pipes perform. This article defines heat pipes and outlines their components, types, applications, and performance factors.
What Is a Heat Pipe?
A heat pipe transfers heat by cycling a fluid between evaporation and condensation states in a sealed enclosure. Heat pipes are usually used in spacecraft, electronics, and other fields where space, mass, or energy consumption is restricted.
What Is the Function of a Heat Pipe?
A heat pipe's main job is to efficiently transfer heat from a heat source to a heat sink. It can transfer a lot of heat even if the temperature difference is minimal because a phase change is part of the process.
How Do Heat Pipes Work?
Every heat pipe needs a working fluid — usually water or a refrigerant. The fluid absorbs heat, vaporizes, and then moves to the cooler end of the pipe, where it releases heat by condensing back into a liquid. This ongoing cycle enables it to transfer heat over considerable distances. Systems for electronic cooling and heat recovery tend to utilize heat pipes.
What Are the Components of a Heat Pipe?
The following parts make up a heat pipe:
1. Evaporator
The evaporator in a heat pipe absorbs heat from the source and vaporizes the working fluid. The vaporized working fluid will then transfer heat from the source to the condenser.
2. Condenser
When the working fluid releases heat and condenses back into a liquid, it does so in the condenser section of the heat pipe, which is in contact with the heat sink.
3. Wick Structure
The working fluid is typically transported from the cooler end of the heat pipe to the hotter end via capillary action with the aid of the wick structure that lines the interior walls of the heat pipe. Sintered metal powders, woven metal mesh, and porous ceramics are examples of typical wick materials.
What Is the Common Design of a Heat Pipe?
A heat pipe is an enclosed cylindrical metal tube, usually made of copper or aluminum, that contains a wick structure. Heat is transferred efficiently as the working fluid circulates between ends via evaporation and condensation, with capillary action in the wick structure returning the liquid to the heat source.
What Is Heat Pipe Technology?
Heat pipe technology uses sealed tubes with working fluids to passively transfer heat between two regions via phase change, requiring no external energy input.
What Are the Types of Heat Pipes?
Heat pipes come in several different styles:
1. Vapor Chamber Heat Pipes
Heat is transferred to the fluid using a wickless structure in vapor chamber heat pipes. They are commonly employed in cooling solutions for CPUs, GPUs, LED lighting, and other high-power electronics. While these versions have uniform temperature distribution and the ability to cool multiple devices, they are relatively expensive and typically require that the evaporator and condenser lie on the same flat plane, though some designs can manage multidirectional heat flow. The absence of a wick is the primary distinction between vapor chamber heat pipes and conventional heat pipes.
2. Variable Conductance Heat Pipes (VCHPs)
Variable conductance heat pipes (VCHPs) are heat-transfer systems that move heat using a working fluid and a non-condensable gas (NCG). VCHPs are used in energy systems, spacecraft, and electronics. They have benefits like high heat transfer rates, passive operation, and orientation flexibility. They do, however, come with a few drawbacks, such as high manufacturing costs and a more complex design than conventional heat pipes. Unlike conventional heat pipes, VCHPs include a conductance mechanism that regulates heat transfer based on the temperature difference between the evaporator and condenser.
3. Diode Heat Pipes
A diode heat pipe is a heat transfer device that uses internal design features to control and limit heat flow in one direction, mimicking the function of a diode. It comes in two types: Liquid Trap Diodes and Vapor Trap Diodes. They are used when heat flow in the reverse direction needs to be prevented. Furthermore, they are employed for the thermal control of spacecraft and electronics. High heat transfer rates and low power consumption are benefits; a narrow temperature range and sensitivity to orientation are drawbacks.
4. Thermosyphons
A thermosyphon heat pipe is a passive heat transfer device that uses gravity to circulate a working fluid, usually in a closed loop. It is frequently used in solar water heaters and for cooling electronics. Its benefits include ease of use, reliability, and affordability, while its drawbacks include a lack of flexibility and sensitivity to orientation. The mechanism used by conventional heat pipes and thermosyphons to transfer condensate from the condenser to the evaporator is the primary distinction between them. In heat pipes, the condensate returns via capillary action in a wick, whereas thermosyphons rely on gravity.
5. Loop Heat Pipe
A loop heat pipe is a form of heat transfer device that uses a two-phase mechanism to extract heat from a source and passively transmit it to a condenser or radiator. LHPs can operate against gravity and provide dependable performance over greater lengths than heat pipes can. Heat is transferred from a heat source to a heat sink efficiently and without any energy input. Unfortunately, LHPs are complex and expensive. LHPs are employed in industrial operations, electronics cooling, and thermal control of spacecraft.
6. Oscillating or Pulsating Heat Pipe
A passive, two-phase heat transfer device called an oscillating or pulsating heat pipe (PHP) moves heat through capillary action and oscillatory motion. It has uses in the automotive, aerospace, and electronics industries. Its benefits include affordability, low thermal resistance, ease of construction, and effective thermal performance. Numerous consumer electronics, such as smartphones, tablets, and gaming consoles, employ these heat pipes. They help dissipate generated heat, improving the performance and lifespan of the devices. One drawback is the restricted working range. The use of oscillatory motion, which is thermally driven and combined with capillary forces, distinguishes PHP from conventional heat pipes.
What Are the Applications of Heat Pipes?
Examples of heat pipe applications are listed below:
1. Computer Cooling
High-performance computer processors and graphics cards are often cooled with the help of heat pipes. They can enhance the effectiveness and lifespans of these components by removing heat that would otherwise damage sensitive circuits.
2. Aerospace
In aircraft and spacecraft, heat pipes are used to move heat from high-temperature regions to low-temperature regions. They control temperatures and keep machinery from overheating or freezing. Heat rejection on spacecraft is complicated by the fact that they cannot dissipate heat to space via conduction or convection, so they’re limited to radiative cooling and heat pipes shunt thermal energy to the radiators. High thermal conductivity, low weight, and dependability are all advantages in the aerospace setting.
3. LED Lighting
LED lighting systems remove the diodes’ thermal energy using heat pipes. The heat pipe increases the LED's efficiency and lifespan and reduces its overall energy draw.
4. Energy Systems
Energy systems employ heat pipes to effectively move heat from one place to another. They are advantageous because they require little outside energy to operate, have high thermal conductivity, and can move heat over a large area with little thermal loss.
5. Medical Devices
Heat pipes are widely used in consumer electronics, medical devices, and aerospace equipment to transfer heat away from sensitive components and maintain stable operating temperatures.
6. Consumer Electronics
Numerous consumer electronics, such as smartphones, tablets, and gaming consoles, employ heat pipes. They help remove excess heat from these devices, improving performance and extending lifespan.
7. Solar Thermal
In solar thermal systems, heat pipes, especially in evacuated tube collectors, are used to transfer heat from the solar absorber to the heat storage system. These systems are designed for minimal thermal losses, offering efficient heat transfer, low maintenance, and long service life.
Which Type of CPU Cooler Contains Heat Pipes?
Heat pipes are found in many CPU coolers, such as those made by Noctua. Heat is moved from the CPU to the radiator fins with the help of heat pipes so that the fan can dissipate it.
How Are Heat Pipes Used in 3D Printing?
In advanced or industrial 3D printers, heat pipes may be used to stabilize hot end temperatures in extrusion-based systems. While not common in typical FFF printers, they can help reduce thermal fluctuations in high-precision applications.
What Are the Factors That Affect a Heat Pipe's Performance?
Several factors can affect heat pipe performance, including:
1. Heat Input
The heat input determines the rate of phase change in the working fluid. If the input exceeds the heat pipe's capillary or vapor transport limits, dry-out or flooding may occur, reducing efficiency.
2. Operating Temperature
The amount of heat that can be transferred through the pipe depends on its operating temperature, which has an impact on how well the pipe performs in any given situation. Up to a certain point, higher temperatures can improve performance; however, once that point is crossed, the pipe's efficiency begins to decline.
3. Heat Sink Design
The heat sink’s design can greatly influence the effectiveness of the heat pipe. Elements like fin spacing, fin thickness, and the heat sink’s overall size and shape can impact the device’s ability to dissipate heat. For more information, see our Heat Sink guide.
4. Orientation
Orientation affects the return of the liquid via capillary action. Gravity-assisted orientation improves performance, while adverse orientation can lead to reduced capillary return or dry-out in standard designs.
5. Working Fluid
The operating temperature range, thermal conductivity, and vapor pressure of a heat pipe are all influenced by the working fluid, which has an impact on how well it works. The characteristics of different fluids can either improve or restrict the heat pipe's ability to transfer heat.
6. Wick Structure
The wick structure defines the capillary limit and governs fluid return from the condenser to the evaporator. Its material and pore structure critically affect startup time and thermal performance. As previously described, the wick structure governs the return flow of liquid through capillary action and has a major impact on performance.
7. Thermal resistance
Thermal resistance can reduce a heat pipe's ability to transfer heat. Lower thermal resistance leads to improved heat transfer. It is a crucial factor as it impacts the thermal conductivity of the heat pipe system.
8. Size and Shape
The heat pipe’s size and shape affect its functionality because these factors determine the capillary pressure and heat transfer area, which in turn influence fluid flow and heat transfer characteristics. Larger dimensions and complicated shapes can enhance performance, but also create manufacturing and operational difficulties.
9. Environmental Factors
Environmental variables like temperature, pressure, and gravity have an impact on how well a heat pipe works by changing the fluid properties and flow dynamics inside the pipe. The rate of heat transfer and heat-dissipation effectiveness may change as a result of these factors.
What Are the Benefits of Heat Pipes?
Some of the benefits of heat pipes include:
- Enhanced cooling efficiency: Heat pipes are excellent at transferring heat away from a heat source. Electronic and other devices that generate too much heat can thus be efficiently cooled enough to operate properly.
- Reduced energy consumption: Heat pipes are passive devices that require no external power input, helping to reduce overall system energy use.
- Increased lifespan of electronic components: Heat pipes can help increase the lifespans of delicate circuitry and prevent damage caused by overheating by efficiently transferring heat away from electronic components.
- Minimal weight and space requirements: Heat pipes are compact and lightweight. They are an ideal choice for devices where space and weight are limited.
- Improved temperature regulation: Heat pipes maintain stable operating temperatures by rapidly redistributing localized heat, minimizing harmful thermal gradients.
- Silent operation: Heat pipes are passive cooling systems. They operate quietly because they do not need any mechanical parts like fans or pumps.
What Are the Limitations of Heat Pipes?
Heat pipes have some inherent limitations:
- Heat transfer capacity limitation: Heat pipes have a maximum heat transfer capacity, known as the capillary limit, beyond which performance drops significantly. Such circumstances might call for additional cooling mechanisms.
- Orientation sensitivity: Some designs may experience reduced performance if not installed in their intended orientation (see earlier section on performance factors).
- Environmental factors sensitivity: Heat pipes are also highly sensitive to environmental factors such as pressure and temperature, which can affect their performance.
- Limited temperature range: Heat pipes have a limited temperature range over which they operate effectively. Outside this range, their performance may degrade.
- Limited wick structure compatibility: Their use may be restricted in some circumstances because of restrictions on the types of wick structures that function with heat pipes.
- Manufacturing complexity: Heat pipes may not be widely used in some industries because of how difficult they are to manufacture.
Common FAQs About Heat Pipes
Are Heat Pipes Important in 3D Printing Machines?
Yes, heat pipes may be used in high-performance 3D printers to enhance thermal management, particularly for cooling the hot end and preventing heat creep.
Summary
This article presented heat pipes, explained what they are, and discussed their various applications and types. To learn more about heat pipes, contact a Xometry representative.
Xometry provides a wide range of manufacturing capabilities, including 3D printing and other value-added services for all of your prototyping and production needs. Visit our website to learn more or to request a free, no-obligation quote.
Disclaimer
The content appearing on this webpage is for informational purposes only. Xometry makes no representation or warranty of any kind, be it expressed or implied, as to the accuracy, completeness, or validity of the information. Any performance parameters, geometric tolerances, specific design features, quality and types of materials, or processes should not be inferred to represent what will be delivered by third-party suppliers or manufacturers through Xometry’s network. Buyers seeking quotes for parts are responsible for defining the specific requirements for those parts. Please refer to our terms and conditions for more information.
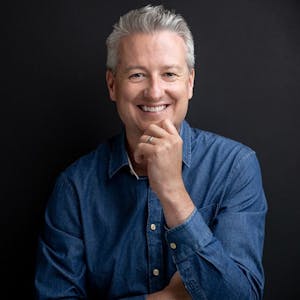